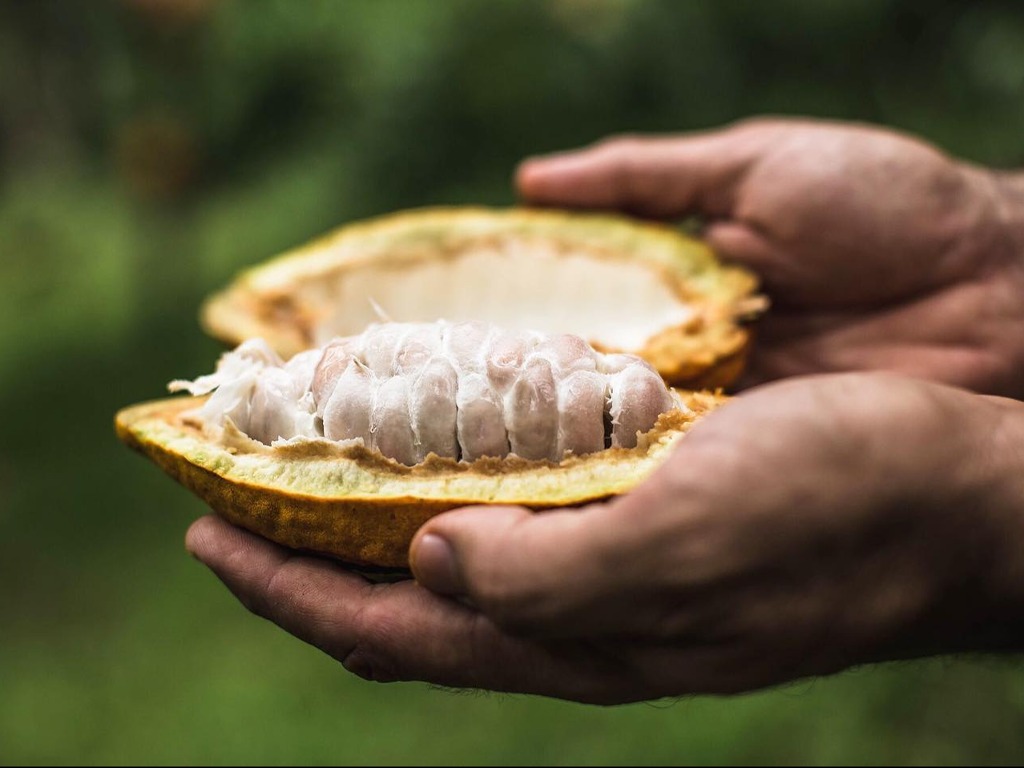
Meet the fifth generation Hawaiian family who are changing chocolate
“I’d like to introduce you to a dear friend of mine. He’s very intelligent, he’s highly evolved, he’s handsome and delicious and very shy,” tour guide Alexandria Webster said mischievously.
“Friends, this is Theo.”
Partially expecting an eligible bachelor to come sauntering around the foliage of the 46-acre Lydgate Farms in Kapaa, Kaua’i, we quickly learn that Theo is short for Theobroma cacao. Alas, not a heartthrob, but a tropical evergreen tree known for its seeds that are used to produce cocoa powder and chocolate, whose scientific name means ‘food of the gods’ in Greek.
“This mood-elevating food was discovered by the ancient Aztecs and Mayans and back then they weren’t nibbling on Hershey,” she says. “They were consuming chocolate as a ceremonial health chocolate tonic beverage and it was fermented cocoa beans with some spices like cinnamon, cardamon, vanilla bean and some hot chilli peppers. If you were drinking it you were likely a monarch or a priest because you were consuming money. This is what they would trade as their currency.”
A superfood with super qualities
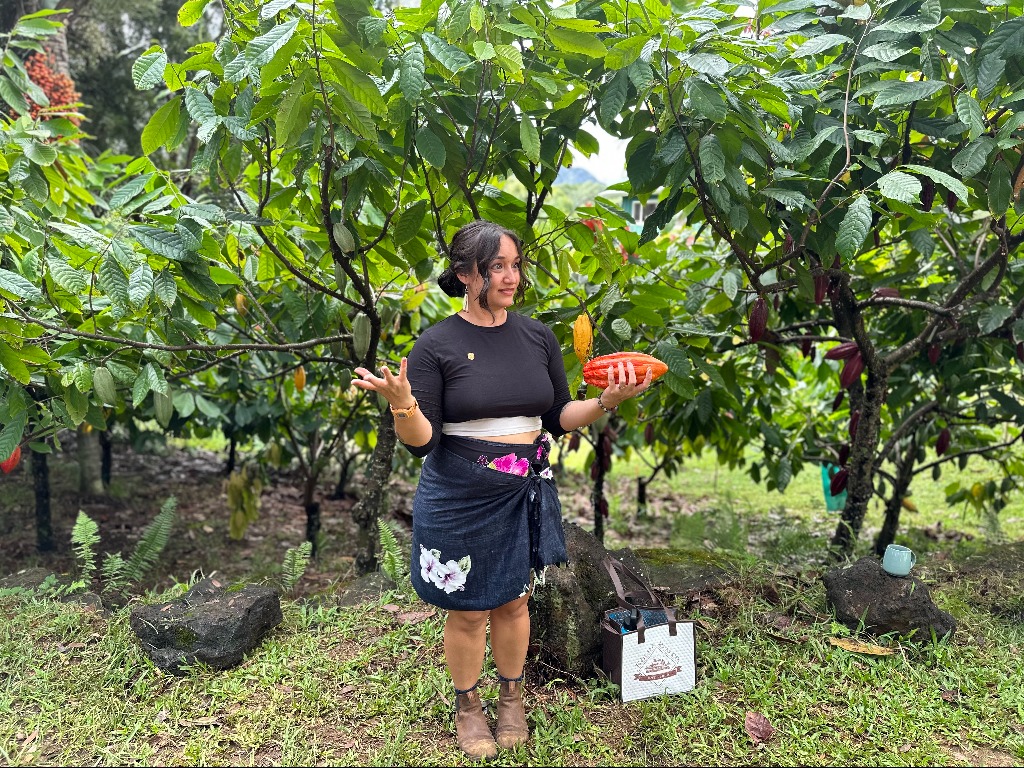
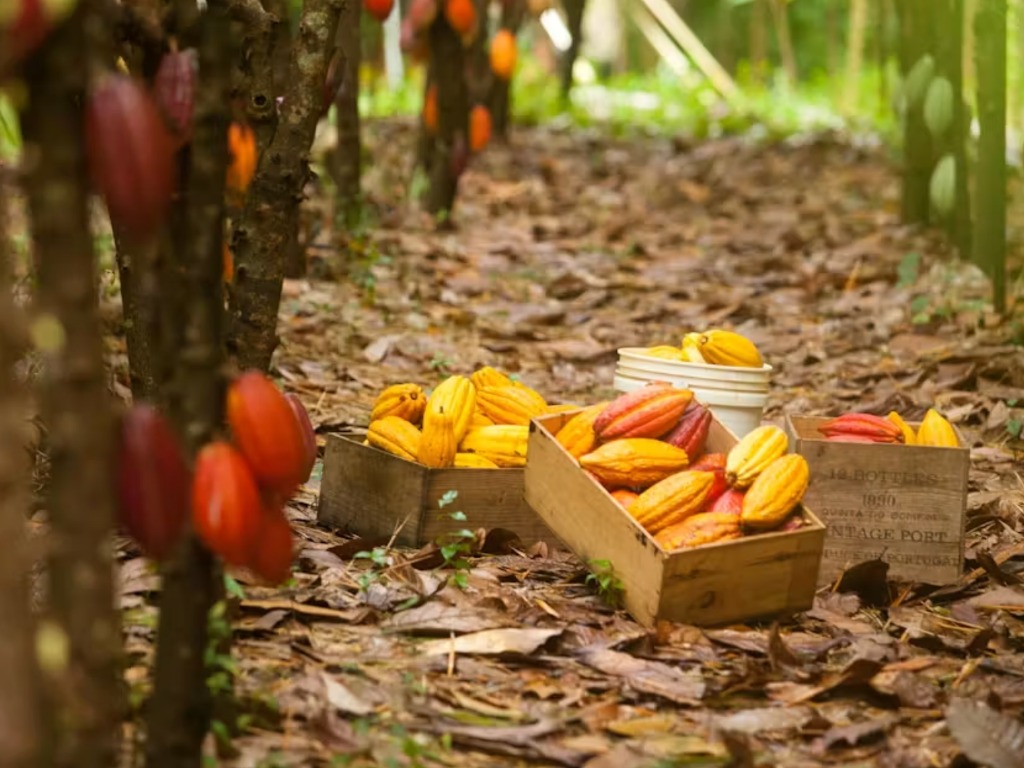
On a mission to change the way people think about chocolate, Webster says many visitors who come to the farm don’t know that chocolate is a fruit.
“It’s not just a fruit, it’s a superfood. Cacao is loaded with vitamins, trace minerals, hundreds of them, it’s one of the highest whole food sources of antioxidants that you can consume. It contains over forty mood-elevating properties,” she said.
Over the centuries, this beverage was used to treat anemia, mental fatigue, tuberculosis, fever, gout, kidney stones, and even poor sexual appetite. While most of the chocolate of today no longer has health benefits, top-of-the line fine chocolates do.
“It only takes one ounce of quality chocolate a day to reap the benefits of heart health, brain health,” she says. “It’s great for your blood circulation, it’s going to open up your vessels, it’s going to improve your mood, your alertness because of the theobromine in chocolate. So, if you eat chocolate every day, you will not only be happier, you’re going to die a little less. It’s shown to lower all-cause mortality.”
Regenerative, generational farming
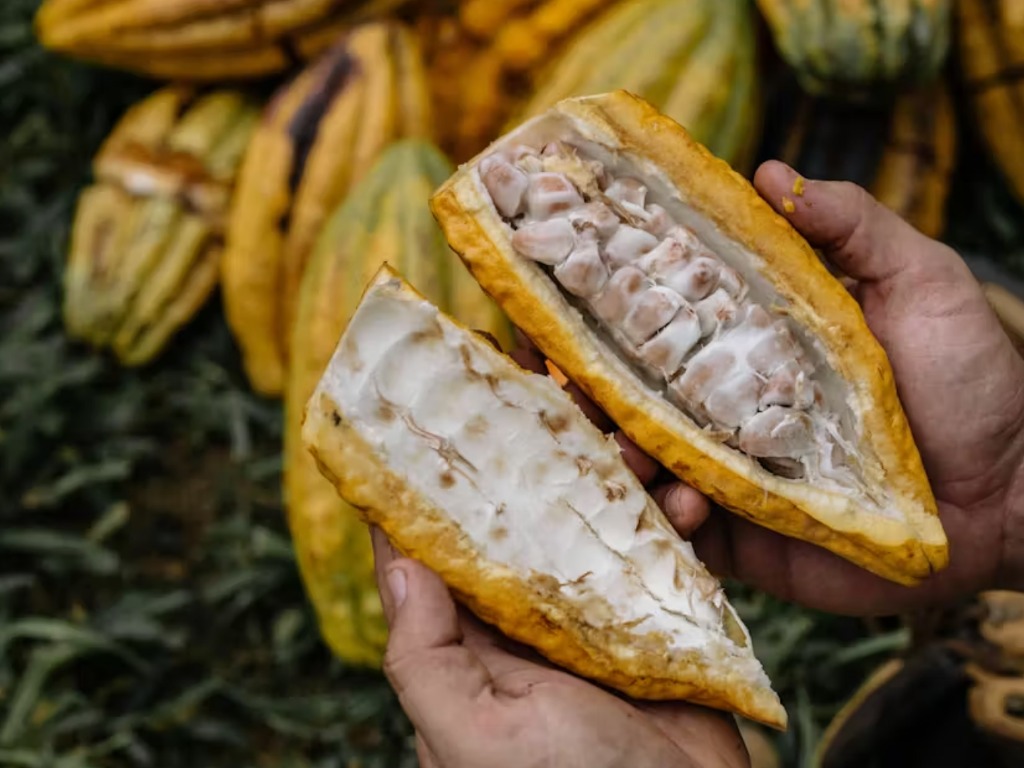
Lydgate Farms is run by Will Lydgate, whose family legacy on Kaua’i can be traced back across five generations. “My great-grandfather William arrived in 1865 with a dream to help build the future of the Hawaiian Kingdom,” he says. “[I’ve] dedicated myself to building a team that grows the best cacao the world has ever tasted.”
Embodying the principle of Mālama ‘Āina, a Hawaiian word that means to care for and honour the land for future generations, sustainability is at the forefront of his efforts. In addition to producing single-estate chocolate and treats like chocolate-covered macadamia nuts, Lydgate Farms also offers vanilla beans and small-batched palm blossom honey.
“This beautiful tropical diverse farm is cultivated in a regenerative fashion, meaning we’re reinvesting in the soil for generations to come,” says Webster, adding that honey tasting is now part of the tour. “Cacao is an equatorial fruit — it only grows about 20° of the equator. That actually makes Hawai’i the only place in the continental US that can commercially grow chocolate.”
The farm has been recognized multiple times for producing some of the best chocolate in the world at international competitions. “Our farm represents the United States of America at the Cocoa of Excellence Awards in Paris. This is a world-wide chocolate competition every two years. Our humble farm is like the Jamaican bobsled team of the chocolate world, the underdogs,” she says, referencing the cult-favourite movie Cool Runnings. “Forty-six acres is a drop in the bucket compared to Ecuador, Peru, Costa Rica, they have thousands of acres and they’ve been doing it way longer than us. Small but mighty, we are now three consecutive runnings of the 50 best tasting chocolates in the whole world.”
From bean to bar
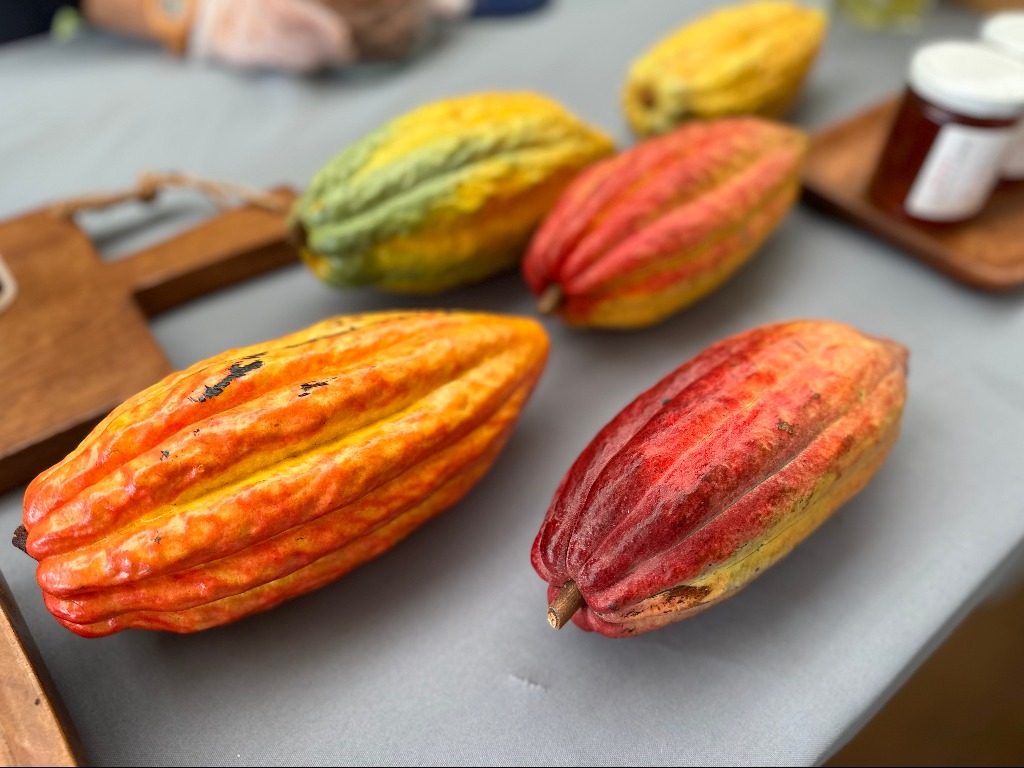
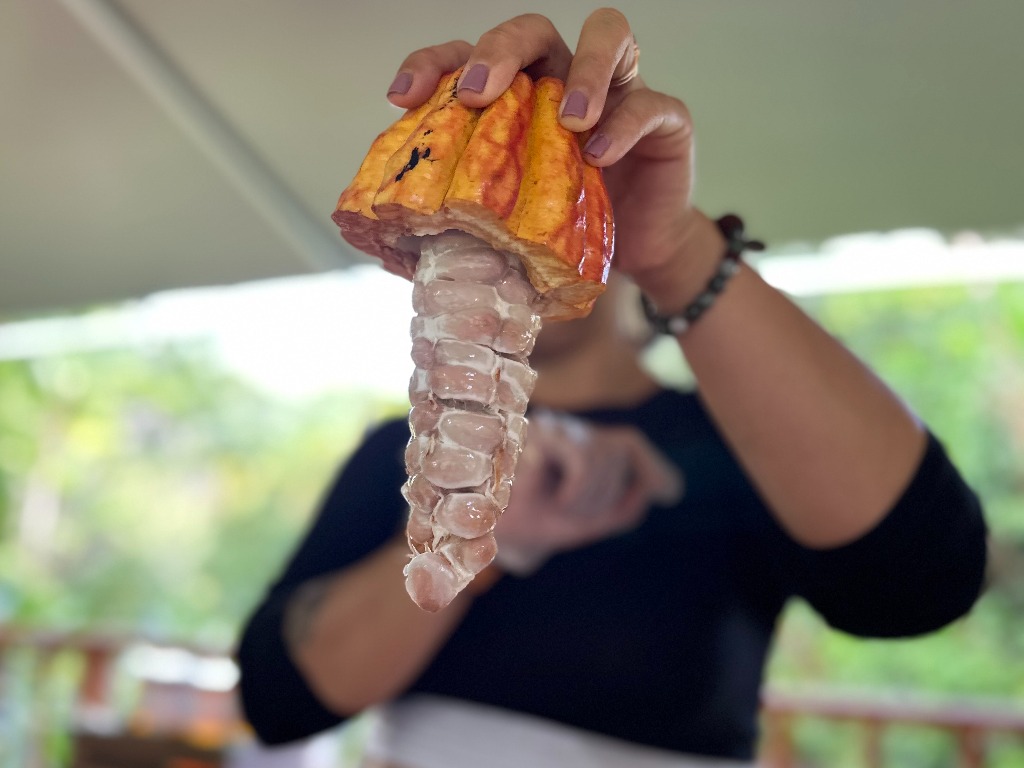
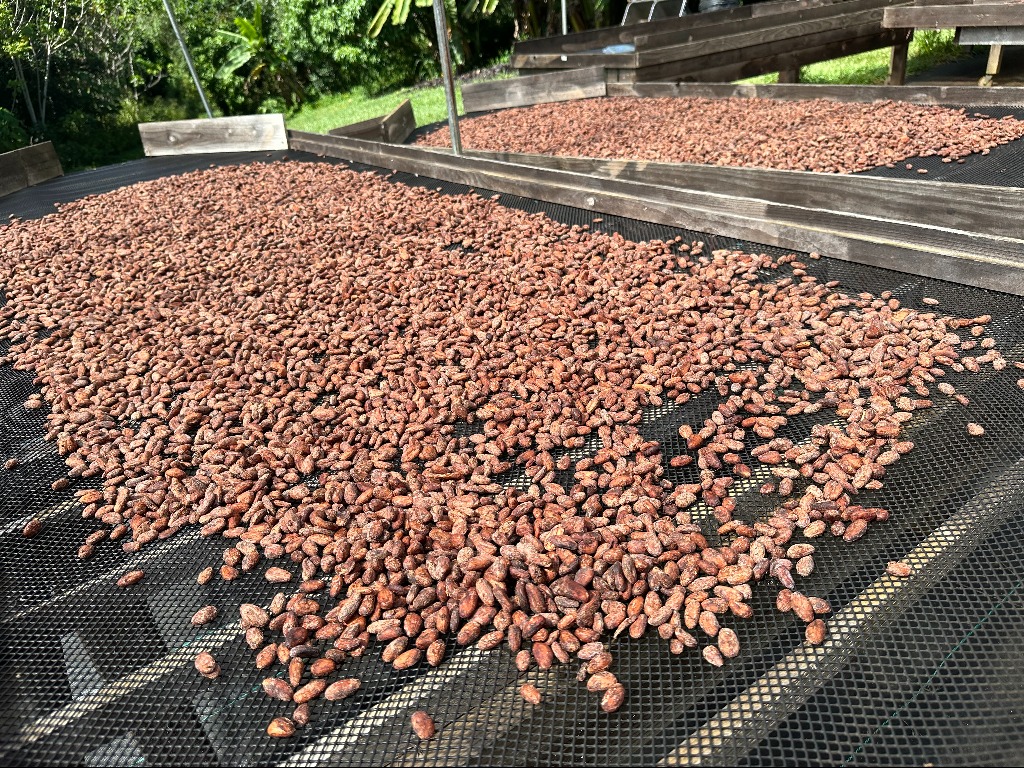
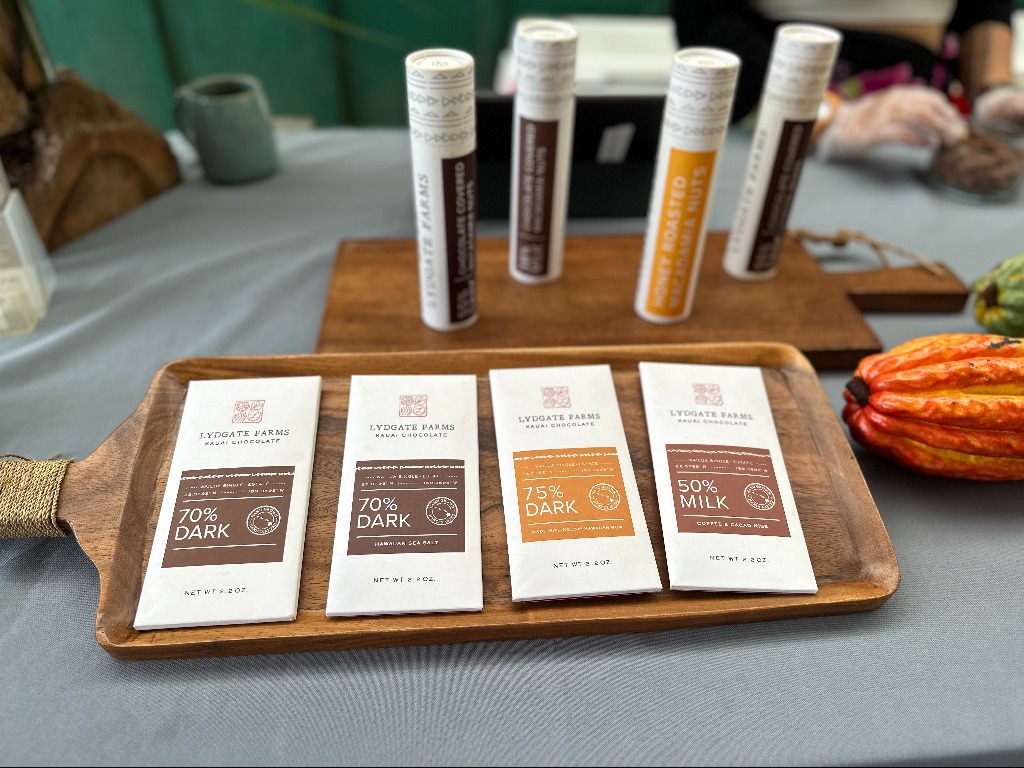
Based solely on the terroir of the farm, chocolate bars can elicit different flavour profiles from fruits to earthy tones. While there are only 14 original families of cacao, they cross pollinate to create thousands of varietals and result in the various coloured pods that range from yellow to vibrant red.
“Chocolate that’s fermented, that has distinctive flavour, that is packed with health benefits, and is not confectionery — meaning it’s heavily diluted with milk and sugar — didn’t even exist until 1997,” she says. “Isn’t that wild? It hasn’t been that long. People are just starting to learn about the art and the science that goes into making fine chocolate. Because Hawai’i is the only state where it can be commercially grown, we’re trying to transform Kaua’i into the Napa Valley of the chocolate world.”
At US$18 a pop, a chocolate bar from Lydgate Farms comes with a heftier price tag than your typical store-bought Cadbury bar. But when you consider the process involved, it should be a lot steeper. “If I crack this seed open and plant a seed today, it takes the tree at least four to five years to start bearing mature fruit. At that age, cocoa blossoms will start to bloom. They are so small that they are not pollinated by bees. They’re pollinated by the midge, which is a type of gnat,” she says. “Then it takes six to eight months for them to mature. A cacao tree can live 50 to 100 years.”
When it’s all said and done, she said the journey from bean to bar takes six to seven years. “Chocolate has more intricacies, more terroir, more flavour markers than wine,” she says.
This story first appeared in the Spring 2024 issue of OFFSHORE. To read the full story, click here.